Introducing the World’s first
biomimetic, tunable,
transparent, and reproducible
3D cell culture well plates.
lates
Technology
We make patented "collagen-like" scaffolds for next generation 3D nanofiber well plates.
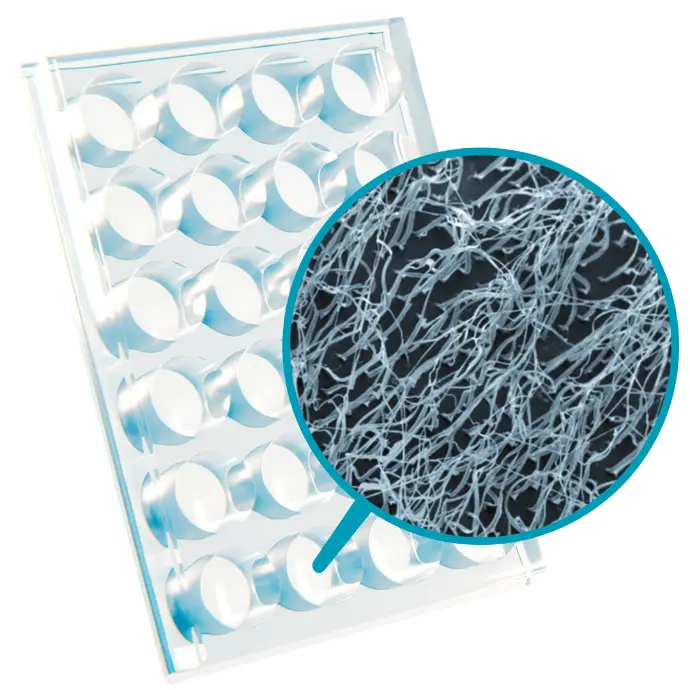
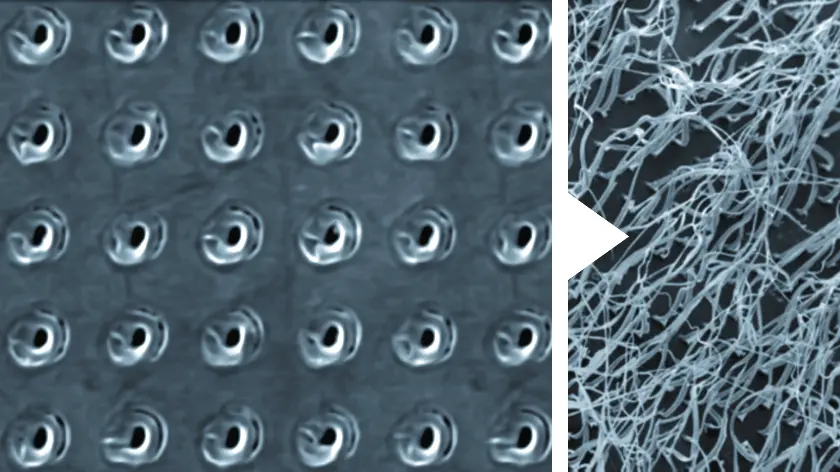
A reusable template or mold is created by drilling billions of cylindrical nanoholes into a glass substrate, placing each hole with 50 nm precision.
The template is used to emboss nanofibers onto a polymer film. The nanofibers form reliably in the template holes, enabling highly precise and customizable fiber spacings and patterns.
Fibers are integrally attached to the film and remain fixed in place.
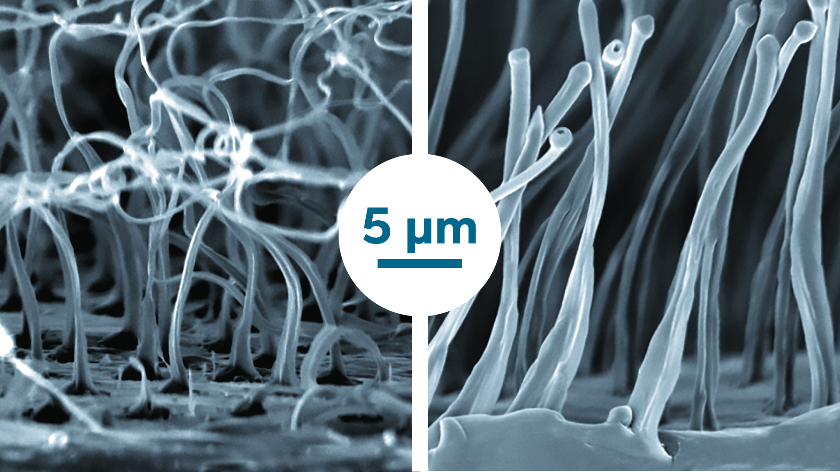
With further processing, fiber diameter (and therefore stiffness) can be increased from a wispy 50 nm to well over a micron.
This provides the means to customize microenvironments across the entire range of collagen fibrils found in biological scaffolds.
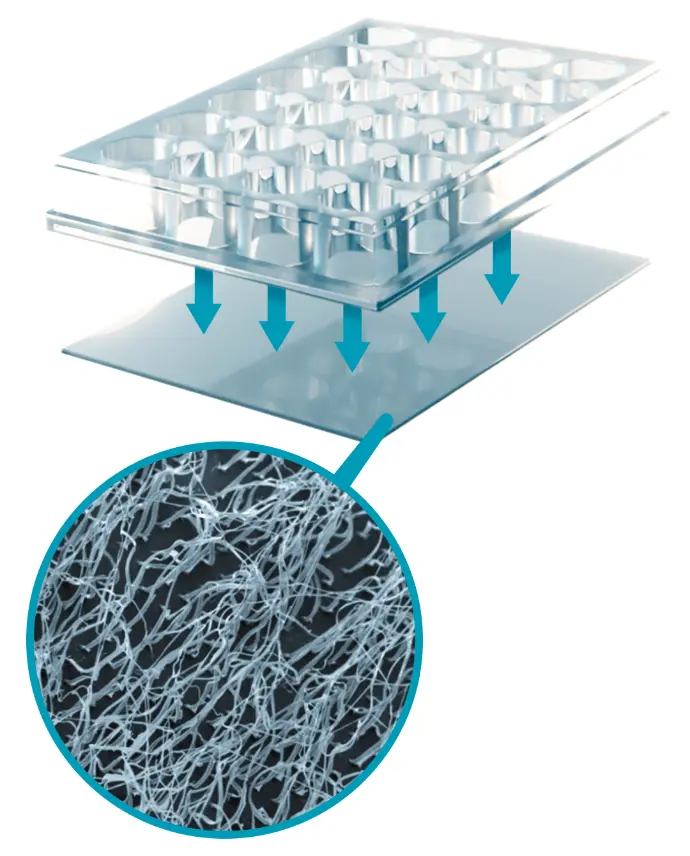
Our 3D nanofiber scaffolds are sealed to the undersides of 2D well plates, which are molded without bottoms but otherwise have standard well plate dimensions.
This allows cell culture to take place in the biomimetic 3D nanofiber microenvironments created by our scaffolds without the need for hydrogels.
These microenvironments are tunable for each application by adjusting the hole patterns and sizes in the template and can be reproduced with high precision.
USF scaffolds are embossed on 125 µm thick polycarbonate cover slips so that cultures can be easily monitored in situ with inverted microscopy.
Other form factors will be available in the future to meet the evolving needs of our customers and the broader marketplace.
3D cell culture scaffolds made from USF nanofilms offer inherent advantages over current 3D scaffolds.
Biomimicry
Collagen-like fiber sizes, spacing/density, orientation, and stiffness gradients create more natural 3D microenvironments for cell culture.
Reproducibilty
Precise control over fiber spacing, size, and stiffness can significantly reduce assay and process variations often caused by the randomness of existing technologies.
Scalability
Batch-producible for fast prototyping, small form factors, and custom lot sizes.
Continuously producible in unlimited quantities, available in rolls wider than 30 cm.
Tunability
Fiber spacing/density, patterns, diameter, shapes, and materials can be customized to optimize conditions for different cell types, with potential to promote:
- Cell health outside the body
- Cell-cell interaction
- Adhesion
- Stem cell maintenance or directed differentiation
- Guided cell growth
- Other specific cell behaviors as needed
Usability
Compatible: Works with standard lab equipment and protocols. Can be functionalized using standard techniques, thin coatings, reagents, or other materials.
Hydrogel-free: Eliminates the need for hydrogels.
Accessible: Open structure allows 360-degree access to cells for nutrients and biochemical signals.
Transparent: Enables in situ imaging for live cell observation.
Convenient storage: Can be stored at room temperature with an extended shelf life.
Versatile: Can be adapted to different form factors beyond well plates, including T flasks, bioreactors, and parallel flow devices.
We can help you achieve your objectives.
Here are two ways to get started .
Sign up to receive free “tuning” well plates
We don’t yet know what fiber densities and other characteristics will work best for your application. The easiest way to get started is for you to first try our “tuning” well plates for free and provide us with your feedback. Each tuning plate will allow you to test six different fiber densities at once.
Depending on your results, you can then either purchase single-density well plates optimized for your application or we can work together to further optimize as warranted.
Arrange a call to discuss your needs.
There is potential to customize microenvironments and form factors for your application.
Click above to arrange a meeting to discuss.
FAQ’s
Yes. In addition to other intellectual property in the U.S. and abroad, we have broad patent protection for both our foundational technology and its application to biology, including U.S. Patents 11,667,062, 11,155,007, and 10,941,380. Other patents are pending.
Nanofibers can be produced with diameters from approximately 50 nm to well over a micron. Fiber spacing can range from less than 3 microns (about 110,000 fibers/mm²) to any desired spacing or pattern. The relative positioning of fibers can be controlled with 50 nm precision. Fiber lengths generally exceed 60 microns for thinner fibers but decrease as fiber diameter increases. Thinner, longer fibers tend to sag under their own weight, with typical "canopy" heights of about 40 microns.
Yes. Patterns can be varied from section-to-section or even fiber to fiber. Each fiber can be placed exactly where it is needed to optimize cell behavior for any given application.
Yes, fiber stiffness can be adjusted by modifying fiber diameter. Material choice also impacts stiffness.
Our nanofiber scaffolds are currently made from polycaprolactone (PCL) on optically clear polycarbonate (PC) film substrates. The thickness of the PC is 125 microns, the equivalent of a #0 coverslip. Cells in the well bottoms only contact PCL, which is a bioabsorbable polymer commonly used in FDA-approved in vivo devices. Our well plates are also made from high quality PC.
Yes. A wide range of polymers have been used for nanofilm production, and others can be developed for future applications. Our technology is generally compatible with most thermoplastics and some thermosets.
No, hydrogels are unnecessary. Our collagen-like nanofibers already provide a superior 3D microenvironment.
Yes, USF nanofilms are compatible with common coatings. poly-amino acids and proteins.
Yes. Our well plates are made to standard dimensions and are compatible with liquid handling systems, microplate readers, robotic systems, and other standard lab equipment.
Yes, cells can be viewed in situ through our optically clear well bottoms. The polycarbonate is equivalent to a #0 coverslip specifically for inverted microscopy.
Not yet, but we plan to offer sterile versions soon. The nanofiber scaffolds are produced from molten polymer at >80°C and attached to well plates in a clean environment but are not yet certified sterile. We recommend cleaning with 70% ethanol/water solution followed by ultrapure water rinsing before use. Once wet, fibers should remain wet to avoid changes in the microenvironment upon drying. We plan to pursue radiation sterilization certification in early 2025.
Yes, our nanofibers are integrally and permanently attached to the underlying substrate. They are extremely difficult to remove, even with a razor blade. PCL fibers are bioabsorbable and may eventually degrade in vivo over weeks or months.
Yes, they can be stored at room temperature. While accelerated aging tests have not yet been conducted, we expect them to age similarly to standard 2D well plates.
Yes, other formats can be developed as needed. We will expand our offerings when there is sufficient demand.
Yes, our nanofiber scaffolds can be integrated into various formats, including T flasks, petri dishes, bioreactors, and parallel flow devices. We can batch-produce or scale up with roll-to-roll methods, producing scaffolds in widths greater than 30 cm. We welcome partnerships to develop applications for different needs.
Yes. We are happy to discuss custom solutions, but we will need to prioritize based on complexity and potential impact. If you're interested in customization, contact us to arrange a discussion.